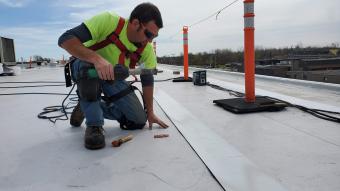
When your roof leaks, you need to have an inspection by a qualified, experienced roofing contractor. Choose an established, credible company that you can trust. Many roofing estimates are free, and most reliable roofers will provide you with a detailed investigation report outlining a summary of observations, written recommendations, other important information along with prices and various options which may be available to help you with your roofing problem.
Every building has its own footprint and characteristics which are unique, and so each flat roofing project requires special considerations, a comprehensive analysis, and site-specific solutions.
During an initial stage of a roofing assessment, the building's history needs to be reviewed. In the case of older structures oft times a seemly safe concrete or brick façade simply masks old materials left behind in previous renovations. These can present hidden structural dangers, worn supporting elements and fire hazards. Examples could be brick over clapboard, or rusted steel supports covered up with other materials.
One technique which helps expose some roofing problems is core sampling. This diagnostic test requires cutting holes deeply through existing flat roofing materials this reveals the history about that particular roof. Then an analysis of the internal building conditions should be made. Results will identify pre-existing issues, such as dry rot, which can indicate structural weakness as well as fire risk. Further examination may also reveal mold--a potential health issue as well as other material failures. Threats such as the presence of designated substances as in asbestos or cold tar pitch may also be discovered and require specialized handling.
Examination of the building structure and design may reveal inadequate engineering or architectural issues which need to be corrected. This might occur in older buildings having a history of numerous renovations or expansion work. Fire walls, parapets or curbs must be checked for wear or cracking and other damages. Visual inspection identifies ponding, poor drainage and roof sponging which may indicate integrity problems with decking or framing.
Assessment of insulation, substrate, and decking is also necessary. Sometimes these materials are stable, and reusable or recyclable which is important from a waste management "green conscience" perspective. It also saves the customer extra disposal expenditures.
Identification of existing roof waterproofing systems is important to determine product synergies. Some of these include Coal Tar Pitch, Bitumen, Rubberized Asphalt, EPDM (Ethylene Propylene Diene Monomer), Polyurethane Foam, and waterproof/liquid coatings. Failure or incompatibility of roofing materials may be a source of problems.
Immediate threats to building integrity and property safety must be given urgent attention. Recommended action will help mitigate further loss or damage until project approval and commencement.
Suitable roofing specifications must be designed for each location. The least hazardous approach to complete the project should be high on the priority list. This includes special considerations for detail work, product suitability, and assessment of any other threats to work performance, such as security of area along with roof accessibility. Often roofing systems and traditional products are not effective due to building anomalies, climatic conditions or local environmental issues. For example, if a building is located in an area where there are high concentrations of air borne contaminations or if the business has its own manufacturing emission issues these could impact the use of various roofing methods. Therefore, site-specific, unique processes or materials may have to be created through controlled experimentation in order to achieve an effective waterproofing result. There is considerable chemistry involved in products and their interactions. Some products will work together, the combined usage of other materials may be unknown. Solving the problem of what to do or what to use is not always straight forward.
Every facet of a flat roofing construction project requires a variety of supplies and accessories such as membrane, insulation, adhesives, sealants, fastening techniques and drainage or ventilation details. Other considerations must include building orientation, prevailing winds, ice or snow loads, along with heat or sun exposure. Building movement, contraction and expansion must also be taken into account along with complex roof details such as skylights, windows, vents, HVAC units, gas lines, cant strips, flashings and other fabricated components. Sometimes unusual details on flat roofs require the research, development and manufacturing of an exclusive mechanism to complete the roofing project.
The above factors must be considered along with budget constraints of a building owner, unique design requirements and finally the necessary materials, tools, specialized equipment and labour for the flat roofing job.
Building owners, physical plant managers and/or property committees should meet with roofing contractors to review the specification and discuss methods, design proposals and product options. Generally the entire process from first viewing the project to completion and an additional warranty period means a long-term relationship between the building owner, roofing contractor and manufacturer of the chosen product-line. Do your own due diligence and choose your roofing contractor wisely!